IntroductionGrabCAD Print is a 3D printing application that lets users prepare 3D models for printing, schedule jobs to 3D printers and then monitor them remotely.
My Role
Back in 2016, I joined the team right as GrabCAD Print was released in beta, and my role as a product designer was to improve the app's overall user experience before the full launch.
I worked alongside other 2 designers, PMs, and developers on the team and was responsible for designing a consistent and intuitive experience for our users.
The Challenge
Before GrabCAD Print, the owners of Stratasys 3D printers had to use three or even four different applications just to prepare and queue jobs to their printers.
Not to mention that the applications had very complicated, inconsistent, and outdated UI, which looked like it was built in the 80s (which, in fact, it probably was…).
The users were unhappy, and it was becoming clear that the software that comes with the printer is just as important as the printer itself.
Stratasys acquired GrabCAD to build better software solutions for 3D printers.
Therefore, our challenge was to design one application with an intuitive workflow and consistent experience for a complicated technology that a wide range of users will use.
Usability Testing
One of the first initiatives I took on was identifying and analyzing usability problems of the application and leading usability testing efforts at GrabCAD. I organized:
1) 1-on-1 user testing sessions
2) user testing events with students at schools
3) visited or called existing users and observed and interviewed them about their processes and workflows.
You can read more about my process in
this article on Medium, but here is the high level:
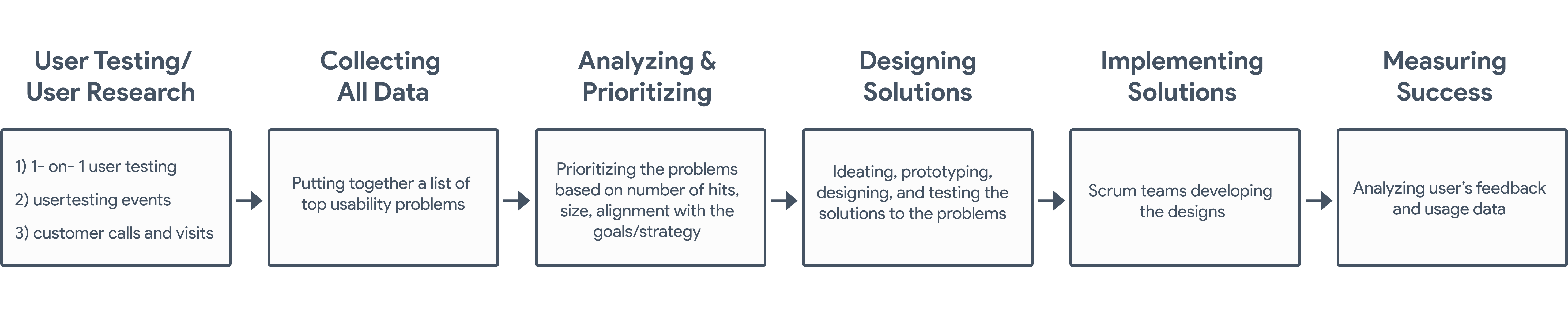
During the usability testing, we have found out a lot of problems with our software. From simple ones like not understanding the meaning of an icon to some of the basic features that the software needed to include.
Next, I collected all the discovered issues, ranked them by the number of times they came up, estimated the approximate size of the problems, and checked how they align with our product strategy and goals.
Then, I presented them to the whole team while quoting the users and showing that some of those fixes could be low-hanging fruits but would hugely impact the usability of the software. The top ten of the issues were designed, implemented, and released in the product in the next six months. (Yay!) Some were as easy as redesigning a confusing icon, and some were more complicated, such as adding an important feature like the ability to select multiple models.
Designing Solutions
Here are a few examples of the features I worked on for GrabCAD Print.
Print Job Comments in the Schedule view
The Problem
As a printer operator, I need to communicate to other users that a job is urgent or that I will need to use red material for this job.
Solution
Comments can be added to any job in the Schedule view to indicate if a job is urgent, or if the printer operator needs to use a certain material for this job.
The Why
Schedule view is the best place for this feature since all the jobs and printers are visible here. A printer operator can hover over the comments icon and read the comment easily. After I designed this workflow, I called five users, tested the design with them, and got great positive feedback.
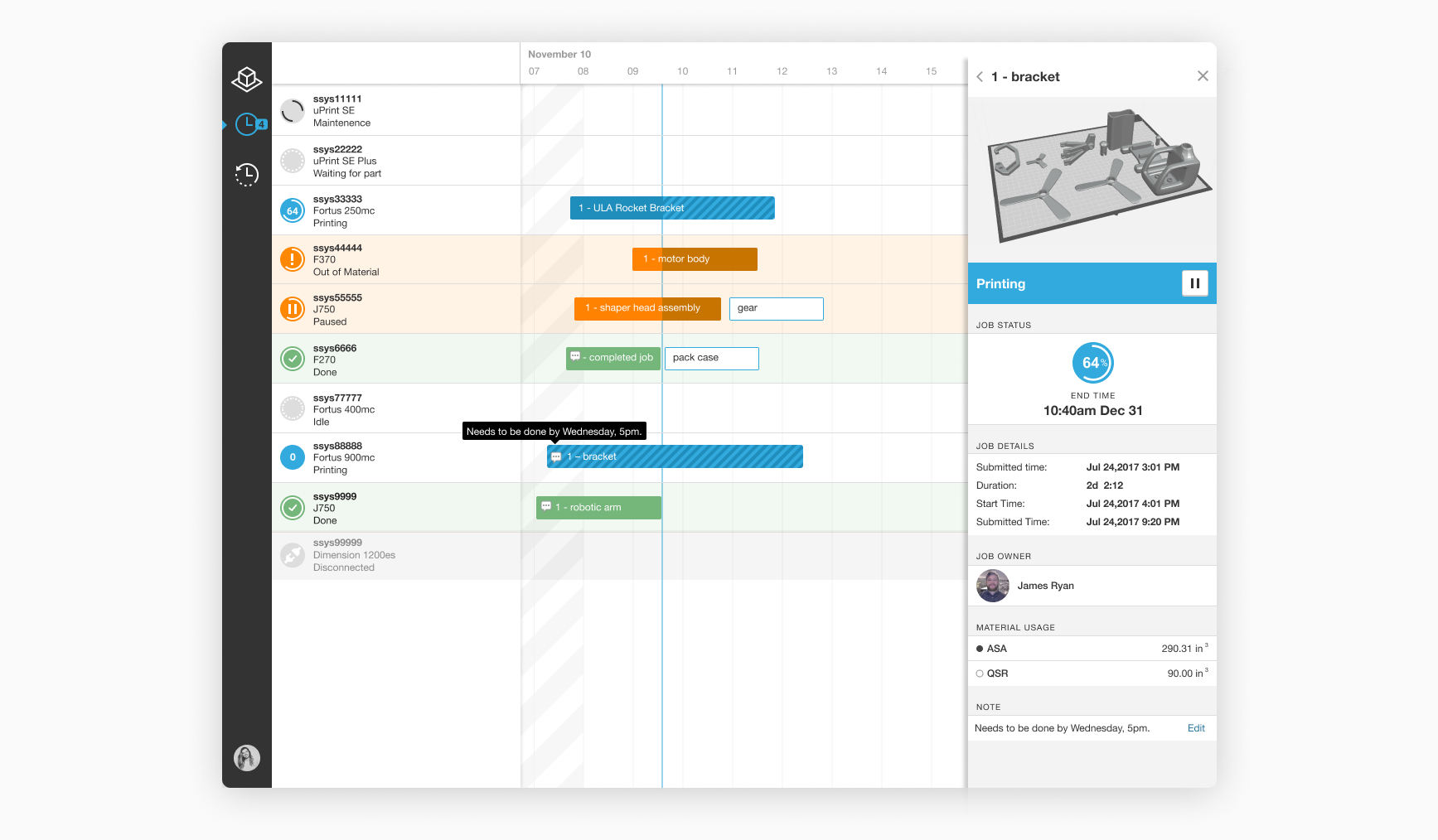
Scheduling a Delayed Print Job Start
The Problem
One of the most powerful Stratasys full-color 3D printers, J750, has a limitation; it has to be cleaned right after the job is done. Otherwise, the heads of the printer will get ruined. Our customers have to find hacks to avoid this problem, some come to their offices at 2 am to clean the heads or hire an intern to do it
The Solution
Scheduling the jobs to start at a specific time( and end at a specific time) will let the users make sure the job ends when they are in the office.
The Why
The solution is allowing the user to schedule the job for the delayed start as their last step of the workflow before the job gets queued. The user can also edit the time in the schedule view, because Printer Panel on the right is what the printer operator uses the most often, so it will be very convenient for him/her to edit the time there.
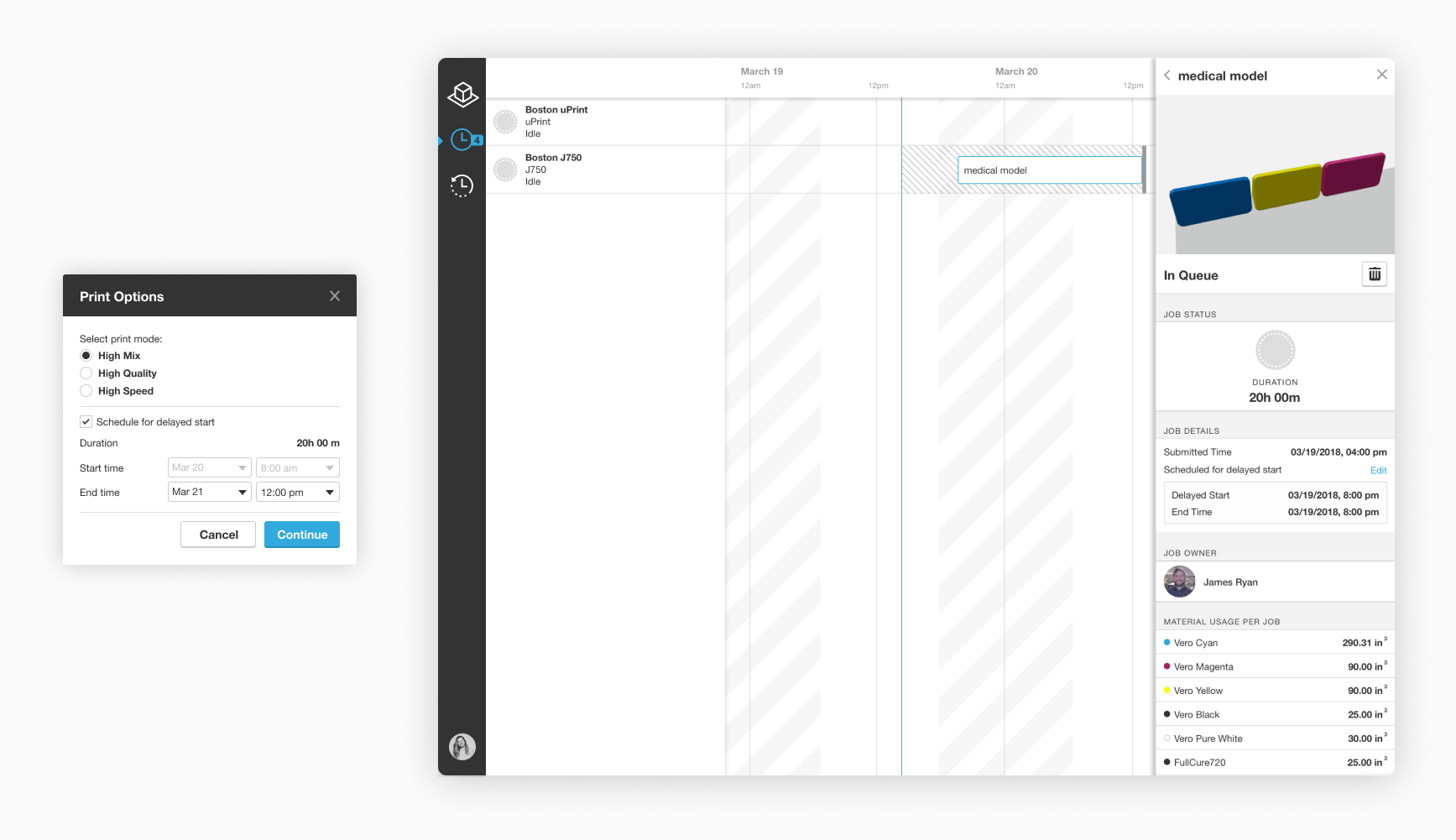
Materials Remaining Redesign for the Printer Panel
The Problem
A printer operator needs to understand how much material left on the printer to know which printer to queue the job to. The printer operator also needs to know how much material will be left on the printer after the job is completed and if s/he needs to schedule another job.
The Solution
The printer panel in the schedule view shows the current material level and the material level at the end of the job on hover.
The Why
Before the redesign, the panel only showed the current material on the printer, and for color printers it already take a lot of space. I wanted to integrate the solution into the existing visual UI that our users are used to and used the diagonal lines to indicate the job.
A fun comment we received from a happy user:
"The area in the lower right of the GrabCAD Print queue is wonderful. I'm referencing the area which shows you the used vs total material for the selected part and the used vs total material on the loaded spool. That's such a great feature for scheduling. (Buy that person lunch! No alcoholic drinks though, we're at work.)"
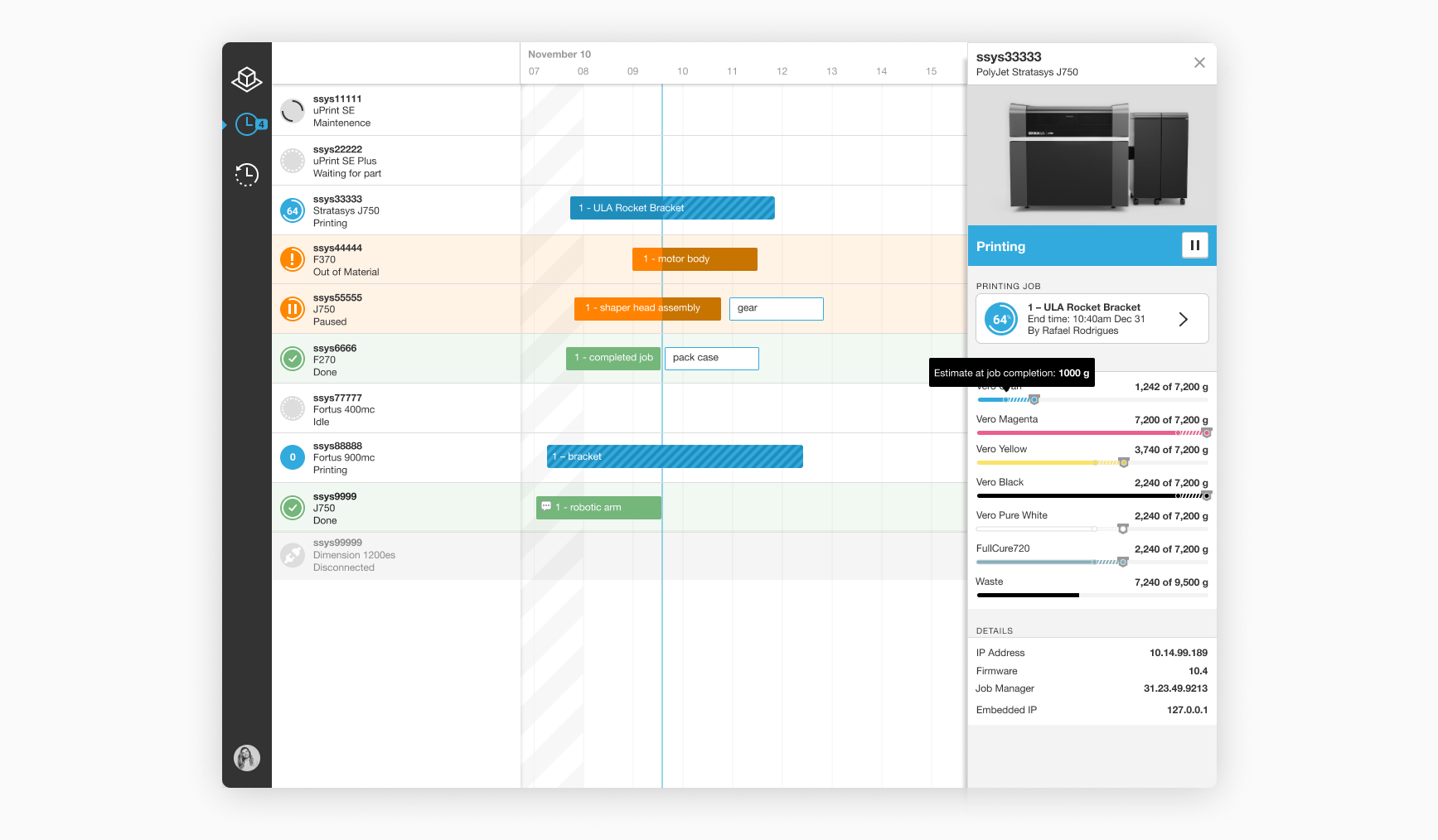
The Outcome
Over the last 2 years since the app was launched, our user base grew from 100 to over 10,000. All over the world, companies like Nike, Ford, Tesla, Boeing, and Disney are using GrabCAD Print to print parts daily. We get amazing reviews, and we keep implementing more features and releasing updates monthly.